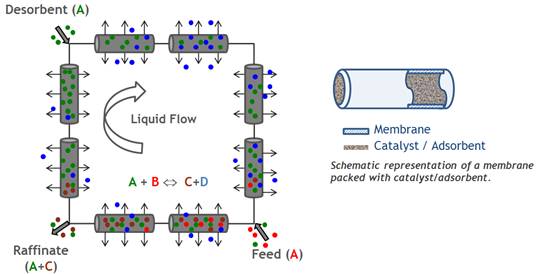
The present invention, in the family of the chromatographic reactors, comprises a reactor with two different separation techniques: a simulated moving bed reactor is integrated with selective permeable membranes.
Reaction and separation in a chemical process are seen, traditionally, as separated steps. However, the combination of these 2 steps in a single device, multifunctional reactors, has gain, due to its advantages, a considerable interest in academic research and in the chemical industry, mainly for equilibrium limited reactions. Multifunctional reactors such as a simulated moving bed reactor unit, have the disadvantage of not being able to easily remove the more adsorbed species, which implies high desorbent consumption. Besides, in several applications, the feed is a mixture of reactants with one of the products which will influence the performance of the unit resulting in low reactants conversion and products purity, low unit productivity and high eluent/desorbent consumption, mainly when the product in the feed is the more retained one.
The simulated moving bed membrane reactor integrates in a single equipment one reaction step with two different separation techniques: chromatography (SMB) and selective permeable membrane (pervaporation or permeation).
The present technology is particularly suitable for the intensification of processes that involve an equilibrium reaction and where more than one product is formed and where the feed is also comprised by one of the products, since they are removed from the reaction zone by adsorption and membranes processes, leading to higher conversions than the equilibrium ones, till almost complete conversion. This technology has potential to produce higher yields of a product, with purity at about 100%.
Consequently, the significant increase in the productivity and considerable reduction of solvent consumption will lower downstreaming, separation units’ costs.
This technology is appropriate for application to the continuous production at industrial scale of oxygenated compounds, as esters and acetals, ethers, ketals, that, by their turn, are used as fuel additives, green solvents, or as intermediates in the production of polymers, perfumes and aromas.