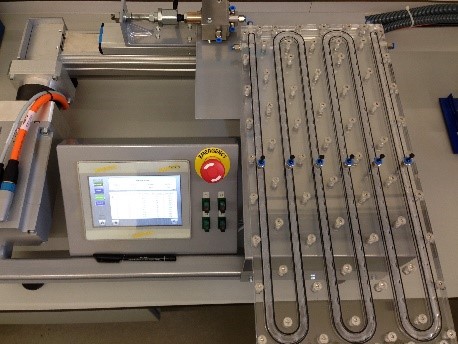
This technology consists in an improved apparatus for mixing intensification in multiphase systems. The technology is based on oscillatory flow mixing (OFM) and comprises an oscillatory flow plate reactor (OFPR) provided with Two Dimension Smooth Periodic Constrictions (2D-SPCs). It has a different geometry and size compared to the common mixing apparatus on the market. The apparatus can be fully thermostatized and it is based on a modular system, in order to achieve most of the industrial application.
Mixing efficiency is the key factor for the success of several processes. Stirred tank reactor is commonly used at industry, however, problems associated with bad mixing, scale up, product quality and process reproducibility, are typically reported. In order to overcome these limitations, associated to the conventional stirred tank reactors, oscillatory flow reactors (OFR) and static mixer are used. Static mixer is characterized by its small size, intense mixing and enhanced mass and heat transfer. However, as the mixing in these units depends on superficial velocity, the desired mixing is, normally, achieved by increasing the fluid flow or mixer units, a disadvantage in some processes. Unlike static mixers, the mixing in OFR can be improved without changing the solution flow and unit numbers, furthermore, it can be operated in batchwise or continuously, flexibility especially relevant to the industry. OFR is basically a column provided with periodic sharp constrictions, called baffles, operating under OFM. The liquid or multiphase fluid is typically oscillated in the axial direction by means of diaphragms, bellows or pistons, at one or both ends of the tube, developing an efficient mixing mechanism where fluid moves from the walls to the center of the tube with intensity controlled by the oscillation frequency and amplitude.
Reagent requirements and waste are significantly reduced due to the size, geometry and ability of this novel OFR to operate at low flow rates. Manufacturing and operating costs are significantly reduced too, compared to continuous stirred tank reactor and available OFR. In terms of productivity, excellent heat and mass transfer is obtained with this novel OFR. The present technology can be assembled and disassembled easily for cleaning and it can even made of disposable material.
Presently, fine chemical, biochemical, biological and pharmaceutical industries that intend to shift from batch to continuous processes, are looking for new devices for mass and heat transfer intensification. This novel OFR is suitable for multiphase applications such as screening reactions, bioprocess, gas-liquid absorption, liquid-liquid extraction, precipitation and crystallization. This novel OFR has been built, tested and is already operating as a mixing apparatus. The scale-up of the technology is in progress.